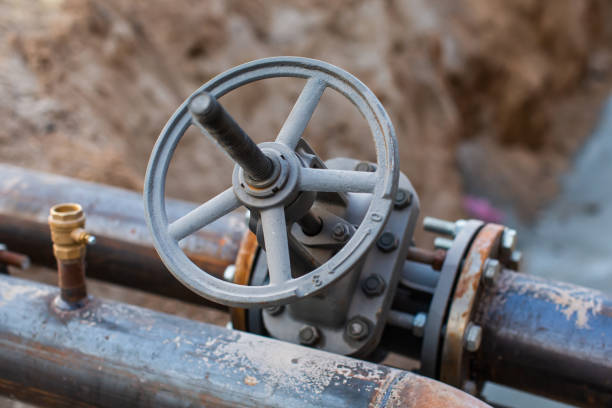
Adjustable Needle Choke Valve
The engineering art of precision flow control
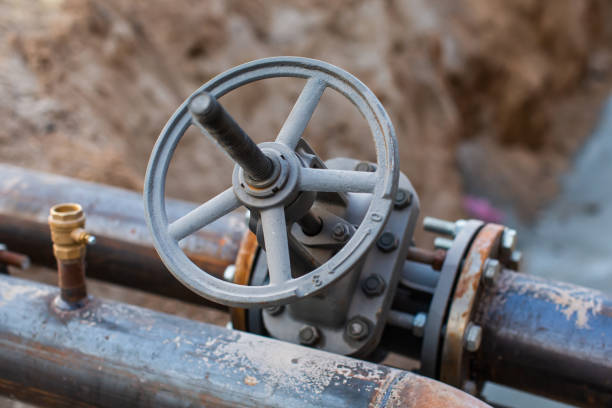
In industrial fluid systems, the precise control of flow and pressure is like the conductor of a symphony orchestra, which not only ensures the release of surging power, but also maintains the absolute stability of the system. The adjustable needle choke valve is the high-precision “baton” in this field. It achieves precise control of fluid media through the linear displacement of the micron-level needle valve core. This article will analyze its technical principles, structural innovations, application scenarios and future trends, revealing how this device protects the safety and efficiency of industrial processes in high-pressure and highly corrosive environments with millimeters.
Peças para campos petrolíferos
- Technical definition and core advantages
The adjustable needle choke valve is a valve that adjusts the flow through the annular gap between the tapered needle valve core and the valve seat. Its core design is that the end of the valve core is slender and conical (the cone angle is usually 10°30°), and linear precision displacement is achieved through thread or hydraulic drive to change the flow cross-sectional area. Compared with traditional throttle valves, its technical advantages are: - Ultra-high adjustment accuracy: the valve core displacement resolution can reach 0.01mm, and the flow adjustment accuracy is ±1%;
- Anti-cavitation and anti-scouring: the multi-stage pressure reduction structure (such as the labyrinth flow channel) can reduce the single-stage pressure difference to below 5MPa, reducing cavitation damage;
- Wide range adaptability: the flow adjustment ratio (Rangeability) is as high as 100:1, which is suitable for continuous control from small flow to high flow rate;
- Bidirectional sealing ability: metal hard seal and elastic soft seal composite design, the leakage level reaches API 598 Class V.
- Structural evolution and key technological breakthroughs
The prototype of the needle throttle valve can be traced back to the pressure reducing valve in the steam engine era in the 19th century, but its real technological breakthrough began with the well control needs of the petroleum industry in the mid-20th century. In 1952, the American Masonelian Company launched the first hydraulically driven needle throttle valve to control the “well kick” phenomenon at the wellhead, laying the foundation for the basic architecture of the modern needle valve.
Equipamento de cabeça de poço
Typical structure of modern needle throttle valve:
Valve core assembly:
Material: The whole is made of Stellite 6 or tungsten carbide (WC) spraying, with a surface hardness of HRC 60 or above;
Structure: The conical needle tip is matched with a multi-stage pressure relief groove to form a stepped pressure drop (such as Fisher’s “Whisper Trim III” design);
Valve seat and valve body:
Valve seat: Overlay welding Inconel 625 alloy, temperature resistance of 540°C, resistance to H₂S corrosion;
Valve body: Forged ASTM A105N carbon steel or F316 stainless steel, diameter range 1/4″4″;
Drive mechanism:
Manual adjustment: equipped with a micrometer dial, the minimum scale is 0.025mm;
Electric actuator: integrated stepper motor and encoder, repeatability accuracy ±0.5%;
Hydraulic drive: output force can reach 50kN, response time <100ms.
Technical Milestones:
In 1987, Norvalve of Norway invented the “dynamic pressure compensation valve core”, which automatically balances pressure fluctuations through fluid feedback;
In 2018, Emerson of the United States launched the “Digital Needle Choke”, which has a built-in MEMS pressure sensor and AI algorithm to achieve adaptive flow control.
Choke Valve / (API 6A Choke Valve)
III. Application Scenarios and Industry Value
The adjustable needle throttle valve is irreplaceable in the following fields:
- Oil and gas extraction:
In shale gas “hydraulic fracturing” operations, the mixing ratio of proppant (ceramsite) and fracturing fluid is precisely controlled, and the error must be <3%;
The throttle valve of the Subsea Xmas Tree needs to withstand a pressure of 15,000 psi and a low temperature of 4°C, and uses a titanium alloy valve body and polyetheretherketone (PEEK) seal. - Chemical and pharmaceutical:
In the microreactor system, adjust the catalyst flow rate to ml/min level to ensure stable reaction kinetics;
When high-purity silane (SiH₄) is delivered, the valve core surface is electropolished (Ra≤0.4μm) to prevent particle shedding and contamination. - Aerospace:
In the rocket engine fuel supply system, the valve needs to work reliably between 253°C (liquid hydrogen) and 3000°C (combustion chamber);
The aircraft hydraulic system adopts a “redundant needle valve” design, and the backup valve automatically takes over when a single valve fails.
According to Market Research Future data, the global high-precision throttle valve market size will reach US$2.9 billion in 2023, of which needle throttle valves account for more than 40%, with an annual compound growth rate of 7.1%.
IV. Technical Challenges and Innovation Directions
- Material Revolution under Extreme Conditions:
In supercritical CO₂ flooding systems, medium temperature is greater than 150°C and pressure is greater than 73.9MPa, and traditional metal valve cores are prone to stress corrosion cracking. Solutions include:
Adopting yttrium-stabilized zirconia (YSZ) ceramic valve core with a hardness of HV 1200 and a temperature resistance of 1600°C;
Diamond-like carbon (DLC) coating is deposited on the surface of the valve seat, and the friction coefficient is reduced to 0.05. - Intelligent and digital integration:
Digital twin technology: ANSYS Fluent is used to simulate the flow field distribution and optimize the valve core cone angle and pressure relief groove layout;
Edge computing module: Integrate FPGA chip inside the valve body to calculate the flow pressure difference curve in real time (such as Schlumberger’s “IntelliChoke” system). - Miniaturization and integration:
MEMS micro needle valve: A micro valve with a diameter of 0.1 mm is manufactured using silicon-based micromachining technology for fluid control of gene sequencing chips;
Modular quick-install design: For example, the “QuickSwap” needle valve of Metrix in Switzerland can be replaced online within 5 minutes. - Green manufacturing and sustainability:
Biodegradable sealing materials: Bio-based fluororubber (FKM) developed by Freudenberg in Germany has a 65% lower carbon emission than traditional materials;
Remanufacturing technology: Laser cladding repair of retired valve cores costs only 30% of that of new valves.
V. Conclusion
The history of the development of adjustable needle throttle valves is an epic of human beings taming violent fluids with precision machinery. From the rough copper valves of the steam age to the smart devices of the digital age, its evolution has always been closely linked to the strongest pulse of industrial needs. Driven by energy transformation and intelligent manufacturing, the future needle throttle valve may integrate quantum sensing, self-healing materials and zero leakage technology to become the “nano-level scalpel” for fluid control in the Industrial 4.0 era. Behind every micron-level displacement accuracy, there is the engineers’ persistent pursuit of ultimate control – this may be the deepest romance of industrial civilization.