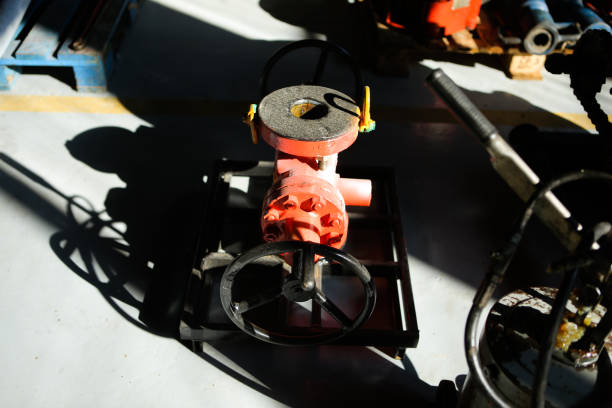
Positive Choke Valve
Equipamentos de petróleo e gás
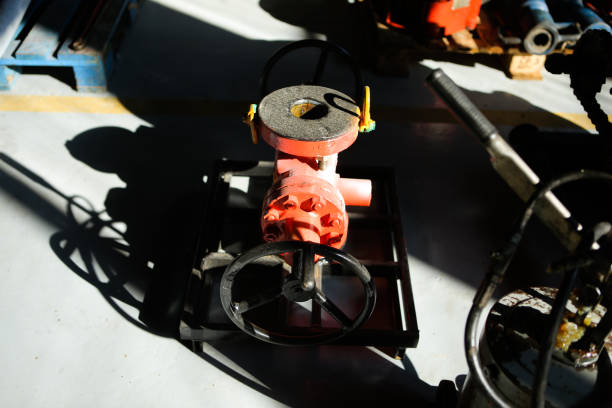
In the field of industrial fluid control, the positive choke valve is like a silent “gatekeeper”, ensuring the safety and efficiency of key industries such as oil, natural gas, and chemical industry by accurately adjusting flow and pressure. As a member of the valve family with higher technical complexity, its design integrates the cutting-edge achievements of fluid mechanics, material science, and automatic control. This article will analyze the unique value of the positive choke valve in modern industry from the perspective of its technical principles, core functions, application scenarios, and development trends.
Peças para campos petrolíferos
1. Technical definition and core functions of positive choke valve
The positive choke valve is a control device that actively limits the cross-sectional area of the fluid channel by mechanical or hydraulic means to achieve flow and pressure regulation. Its “positive” characteristics are reflected in two aspects: first, the direction of valve core movement is coordinated with the direction of fluid pressure to ensure stable regulation under high pressure conditions; second, through mandatory mechanical structures (such as needle valve cores, multi-stage cage sleeves), stepless precision control is achieved to avoid the “cavitation” or “flash” phenomenon caused by pressure fluctuations in traditional throttle valves.
Equipamento de cabeça de poço
Core functions:
1. Flow regulation: Control the medium flow by changing the opening between the valve core and the valve seat;
2. Pressure management: Maintain system back pressure in oil and gas well control and pipeline transportation to prevent pressure loss;
3. Anti-cavitation design: Use multi-stage pressure reduction or carbide coating to extend valve life;
4. Emergency cut-off: Some models integrate fast closing function, and the response time can be less than 50 milliseconds.
2. Structural design and technological evolution of positive throttle valves
The evolution of positive throttle valves is essentially a microcosm of the industry’s response to extreme working conditions. Early simple needle valves are very easy to wear under high pressure difference. In the 1930s, Cameron Company in the United States launched the first multi-stage cage throttle valve, which limited the single-stage pressure difference to less than 5MPa by layered pressure reduction, greatly reducing the risk of cavitation.
Typical structure of modern positive throttle valve:
Valve body and valve core:
The valve body is mostly made of forged alloy steel (such as ASTM A182 F316), with a temperature resistance of up to 540°C;
The valve core design includes needle-shaped, V-shaped ports, porous cages, etc., and the surface is often sprayed with tungsten carbide or ceramic coating to resist wear.
Choke Valve / (API 6A Choke Valve)
Drive mode:
Manual adjustment: suitable for low pressure or auxiliary systems;
Hydraulic drive: provides high thrust for deep-sea oil and gas well control;
Electric actuator: integrated PID algorithm to achieve remote automatic control.
Sealing technology:
Metal-to-metal seals (such as Stellite alloy cladding) are suitable for high temperature and high pressure;
Elastomer seals (such as perfluoroether rubber) are used for corrosive media.
Technology Milestones:
In 1978, the Norwegian Hansen company invented the “TurboChoke” technology, which uses spiral flow channels to convert fluid kinetic energy into rotational motion and reduce turbulent noise;
In 2005, Schlumberger of the United States launched the “EverGreen” intelligent throttle valve, which has a built-in pressure sensor and adaptive control system to achieve dynamic pressure compensation.
III. Application Scenarios and Industry Value
The positive throttle valve is the “lifeline equipment” of the energy and process industries, and its application scenarios cover three major areas:
1. Oil and gas extraction:
In drilling operations, the throttle valve prevents blowouts by adjusting the wellhead back pressure. For example, when hydraulic fracturing shale gas, the fracturing fluid flow rate of 1020 cubic meters per minute must be controlled, and the error must be less than 2%;
The deepwater throttle valve equipped with the Subsea Xmas Tree must withstand a pressure of 15,000 psi and a low temperature of 4°C.
2. Chemical process control:
In the ethylene cracking unit, the positive throttle valve adjusts the quench oil flow to ensure that the cracking gas is quickly cooled to below 300°C;
When transporting highly corrosive media (such as hydrofluoric acid), Hastelloy C276 valve body and polytetrafluoroethylene lining are used.
3. Power and water treatment:
The main steam system of a nuclear power plant uses a throttle valve to control the steam pressure of the secondary circuit to ensure the safe operation of the turbine;
The throttle valve at the front end of the high-pressure reverse osmosis (RO) membrane for seawater desalination needs to accurately maintain an operating pressure of 68MPa.
According to Global Market Insights, the global throttle valve market size will reach US$4.8 billion in 2023, of which the positive throttle valve will account for more than 35% due to its high technical barriers.
IV. Technical Challenges and Future Trends
1. Adaptability to Extreme Working Conditions:
With the development of deep-sea oil and gas fields (such as the Brazilian subsalt oil fields) and ultra-deep wells (depth exceeding 8,000 meters), valves need to work stably at 250°C and 25,000psi. Solutions include the use of powder metallurgy valve cores and nano-composite sealing materials.
2. Intelligent Upgrade:
Digital Twin Technology: Predict valve wear through virtual models, such as GE’s Digital Choke Valve system, which can warn of failures 30 days in advance;
Edge Computing: Integrate a microcontroller inside the valve body to optimize the flow curve in real time and reduce response delays.
3. Green Manufacturing and Circular Economy:
The EU Industrial Emissions Directive (IED) requires valve leakage rates to be less than 100ppm, promoting the popularization of low-emission (LowE) sealing technology;
Modular design: For example, the “QuickSwap” throttle valve launched by the Norwegian SST company can replace the valve core without stopping the machine, reducing maintenance carbon emissions.
4. New material revolution:
Graphene-enhanced ceramic valve seat: friction coefficient reduced by 60%, life extended to 100,000 hours;
Shape memory alloy (SMA): valve core can automatically fine-tune the opening according to temperature to improve control accuracy.