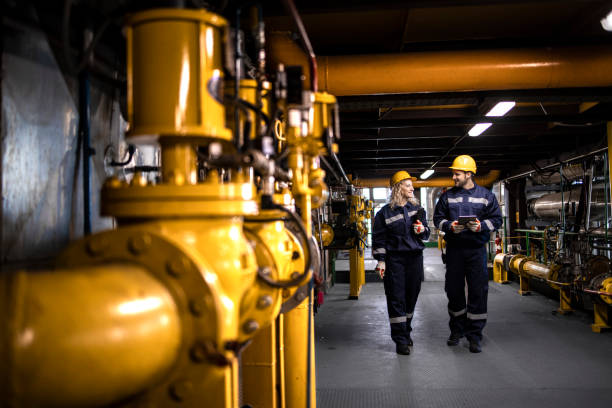
Soft Seated Floating Ball Valve
Equipamentos de petróleo e gás
Soft-sealed floating ball valve, an innovator of precision fluid control
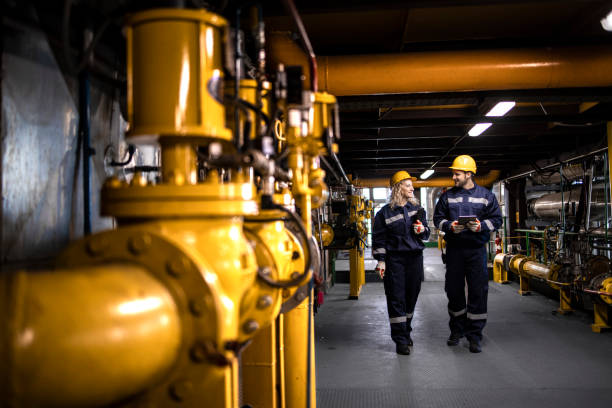
In industrial fluid systems, valves are like “traffic police”, precisely regulating the flow direction, pressure and flow of the medium. Among them, the soft-sealed floating ball valve has become a core control element in the fields of petrochemicals, food and medicine due to its excellent sealing performance and wide applicability. This article will analyze its technical principles, structural innovations, application scenarios and future challenges, revealing how this type of valve redefines the reliable management of industrial fluids through the co-evolution of materials and design Soft Seated Floating Ball Valve.
Peças para campos petrolíferos
1. Technical definition and core advantages of soft-sealed floating ball valve
The soft-sealed floating ball valve is a valve that achieves sealing through the close fit between the floating ball and the elastic valve seat. Its core feature is that the valve seat is made of non-metallic soft materials (such as PTFE, nylon, rubber), and the ball produces a small displacement under the pressure of the medium, pressing the valve seat to form a sealing surface. Compared with metal hard seal valves, the core advantages of soft seal design are:
1. Zero leakage seal: soft valve seat can compensate for the microscopic unevenness between the ball and the valve seat, and the leakage level can reach VI level at room temperature (ANSI/FCI 702 standard);
2. Low operating torque: the friction coefficient is 60%-80% lower than that of metal seal, and it is suitable for light actuators;
3. Corrosion resistance: suitable for corrosive media such as acids, alkalis, and organic solvents;
4. Economical: the manufacturing cost is 30%-50% lower than that of hard seal valves.
2. Structural evolution and key technological breakthroughs
Equipamento de cabeça de poço
The development history of soft seal floating ball valves is a history of collaborative innovation of materials science and mechanical design. In the 1950s, the industrial mass production of polytetrafluoroethylene (PTFE) laid the foundation for soft seal technology. In 1967, DuPont of the United States developed enhanced PTFE (such as Rulon®), which increased the upper temperature limit of the valve seat from 150°C to 230°C through glass fiber filling, greatly expanding the scope of application.
Typical structure of modern soft-seal floating ball valve:
Floating ball: The ball is connected to the actuator through the valve stem, and the medium pressure pushes the ball to move toward the outlet valve seat to form a self-tightening seal;
Válvula
Elastic valve seat:
Material selection: PTFE (corrosion resistant), PEEK (high temperature resistant), NBR (oil resistant);
Structural innovation: The dual lip design (Dual Lip Seat) can pre-tighten the seal at low pressure and strengthen it again at high pressure;
Anti-blowout valve stem: The bottom-mounted structure (BB type) is adopted, even if the valve stem seal fails, the medium will not leak out;
Fire safety design: After the soft-seal valve seat is burned, the metal auxiliary seal ring (such as Inconel 718) can still maintain a short-term seal (API 607 standard).
Technical Milestones:
In 1983, Germany’s KSB launched the “VarioTect” valve seat system, which achieves a dynamic balance between sealing force and medium pressure through spring preload;
In 2012, Japan’s Kitazawa Valve (KITZ) developed the “Superloy” coated ball, with a surface hardness of HRC 70 and a wear resistance increased by 5 times.
III. Application Scenarios and Industry Value
Due to its “clean, reliable and flexible” characteristics, the soft-seal floating ball valve occupies a dominant position in the following fields:
1. Chemical and pharmaceutical:
In the chlor-alkali industry, PTFE valve seats can withstand strong corrosion from wet chlorine (temperature ≤120°C);
The bioreactor pipeline adopts CIP (cleaning in place) design, and the valve flow channel has no dead corners, which meets FDA hygiene standards.
2. Food and Beverage:
The chocolate delivery pipeline uses EPDM valve seats, which are resistant to oil and fat and have no toxic migration;
The aseptic filling system uses electrolytically polished 316L stainless steel valve bodies with a surface roughness of Ra≤0.8μm.
3. Water treatment and energy:
In the pretreatment stage of seawater desalination, valves need to resist chloride stress corrosion, and duplex stainless steel (such as S31803) valve bodies become the first choice;
In the storage and transportation of liquefied natural gas (LNG), deep-cold ball valves use glass fiber reinforced PTFE valve seats that can withstand low temperatures of 196°C.
According to statistics from McIlvaine, the global industrial valve market size will exceed US$85 billion in 2023, of which soft-sealed floating ball valves account for about 18%, with an annual compound growth rate of 6.2%.
IV. Technical Challenges and Innovation Directions
1. Breakthrough of high temperature and high pressure limits:
Traditional soft sealing materials are prone to thermal degradation above 260°C. Solutions include:
Using polyetheretherketone (PEEK) composite materials with a temperature resistance of up to 310°C;
Developing metal-nonmetal composite valve seats, such as graphite embedded in a stainless steel skeleton, which takes into account both elasticity and temperature resistance.
2. Particle media wear protection:
In the coal chemical gasifier feeding system, the surface of the carbide (WCCo) sprayed sphere can resist coal powder erosion;
Self-cleaning valve seat design, such as the “Swinging Seat” technology of Italy’s OMAL, uses the medium flow to automatically remove particle deposits.
3. Intelligent and digital integration:
Embedded sensors: Real-time monitoring of valve seat wear and sealing status (such as Emerson’s ValveLink software);
Digital twin model: Optimize flow channel design through ANSYS simulation to reduce cavitation risks.
4. Green manufacturing and recycling:
Bio-based valve seat material: PEF (polyethylene furandicarboxylate) developed by Avantium of the Netherlands can replace PTFE, reducing carbon footprint by 50%;
Modular valve seat quick-change system reduces maintenance downtime and material waste.
V. Conclusion
The technological evolution of soft-seal floating ball valves is essentially a microcosm of the industry’s eternal pursuit of “reliability and efficiency”. From the innovation of PTFE’s molecular structure to the support of smart sensors, every breakthrough is redefining the boundaries of fluid control. Under the wave of carbon neutrality and Industry 4.0, this field may usher in a deeper material revolution and digital integration – perhaps in the future, self-repairing valve seats and bionic sealing structures will become the norm, and soft-seal floating ball valves will continue to protect every process of industrial pulsation with their precision and toughness.